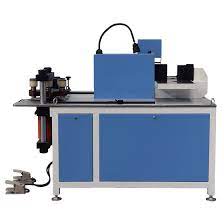
In the dynamic landscape of modern manufacturing, innovation stands as a guiding force, reshaping industries and enhancing production capabilities. Among the impressive array of technological marvels, the bending machine emerges as a true game-changer, redefining the way metal fabrication and other materials are shaped and formed. busbar machine, also known as press brakes, have seamlessly integrated precision, efficiency, and versatility into manufacturing processes, solidifying their role as indispensable tools for various industries.
At its core, a bending machine is a mechanical apparatus designed to reshape sheet metal or other materials into desired angles and contours. Traditionally, such tasks were labor-intensive, requiring skilled artisans to meticulously shape metals by hand. However, the advent of bending machines has ushered in an era of automation, eliminating the dependence on manual labor and significantly expediting the production timeline.
One of the most remarkable features of bending machines is their precision. Equipped with advanced computer numerical control (CNC) systems, these machines can achieve highly accurate bends and angles with consistent results. This level of precision is crucial for industries like aerospace, automotive, and electronics, where even the slightest deviations can lead to compromised product integrity.
Furthermore, bending machines boast remarkable versatility. They can handle a wide range of materials, from thin sheets to heavy-duty plates, and can be equipped with various tools and dies to accommodate different bending requirements. This adaptability empowers manufacturers to swiftly transition between different production runs without requiring extensive retooling, leading to substantial time and cost savings.
The integration of automation and software has not only streamlined the bending process but has also enhanced safety in manufacturing environments. Workers are now less exposed to hazardous tasks, minimizing the risk of accidents and injuries. Additionally, the data-driven nature of modern bending machines enables real-time monitoring, allowing operators to detect issues early on and optimize the production workflow.